Nonwoven cut machines are equipped with various safety features to ensure the safety of operators and prevent accidents during the cutting process.
Here are some common safety features found in nonwoven cut machines:
Emergency Stop Button: Nonwoven cut machines are typically equipped with easily accessible emergency stop buttons. Pressing this button immediately halts the machine's operation in case of an emergency or hazardous situation.
Safety Guards: Safety guards are physical barriers or enclosures that prevent access to the cutting area while the machine is in operation. They are designed to protect operators from coming into contact with the moving parts, blades, or cutting mechanisms. Safety guards are usually interlocked, meaning the machine cannot operate if the guards are not properly in place.
Interlocks: Interlocks are safety mechanisms that ensure certain conditions are met before the machine can operate. For example, the machine may require all safety guards to be securely closed or the operator to be in a safe position before initiating the cutting process. Interlocks help prevent accidental or unauthorized machine activation.
Safety Sensors: Nonwoven cut machines may incorporate safety sensors, such as presence sensors or light curtains, to detect the presence of operators or objects in the danger zone. If an object or person is detected within the restricted area, the machine automatically stops or prevents the cutting process from initiating.
Overload Protection: To prevent damage to the machine or its components, overload protection mechanisms may be implemented. These mechanisms monitor the cutting force or power consumption and automatically stop the machine if it exceeds the safe operating limits.
Safety Labels and Signage: Nonwoven cut machines typically have safety labels and signage placed in visible locations to provide important safety instructions, warnings, and precautions. china nonwoven cut machine These labels help operators understand the potential hazards, safe operating procedures, and emergency shutdown procedures.
Lockout/Tagout (LOTO): Nonwoven cut machines may have lockout/tagout provisions to ensure that energy sources are properly isolated and secured during maintenance or service. Lockout/tagout procedures prevent accidental startup or release of stored energy while personnel are working on or near the machine.
It's essential for operators to receive proper training on the safe operation of nonwoven cut machines and to follow all safety guidelines and procedures provided by the manufacturer. Adhering to these safety measures helps minimize the risk of accidents and injuries when working with nonwoven cut machines.
How can operators receive proper training on the safe operation of nonwoven cut machines?
Operators can receive proper training on the safe operation of nonwoven cut machines through the following methods:
Manufacturer's Training: The equipment manufacturer or supplier often provides training programs or resources specifically tailored to their nonwoven cut machines. This training can be conducted on-site at the manufacturer's facility or at the operator's location. It typically covers machine operation, safety features, maintenance procedures, troubleshooting, and best practices for safe and efficient operation.
User Manuals and Documentation: Nonwoven cut machines are accompanied by user manuals and documentation that outline the machine's operation, safety guidelines, maintenance procedures, and troubleshooting instructions. Operators should thoroughly read and understand these materials to familiarize themselves with the machine's features, safety precautions, and recommended operating procedures.
On-the-Job Training (OJT): Experienced personnel or supervisors can provide on-the-job training to new operators. This training involves practical demonstrations, hands-on practice, and guidance on operating the nonwoven cut machine in a safe and effective manner. OJT allows operators to gain real-world experience under supervision and learn from experienced individuals.
Safety Training Programs: Fire departments, trade organizations, or safety training institutes may offer general machine safety training programs that cover various aspects of machinery operation and safety. These programs can provide operators with a broader understanding of machine safety principles, hazard identification, risk assessment, and safe work practices applicable to nonwoven cut machines.
Online Resources and Courses: There are online resources, video tutorials, and e-learning platforms that offer training modules specifically focused on machine operation and safety. These resources can provide operators with the flexibility to learn at their own pace and access training materials conveniently.
Continuous Education and Refresher Courses: It's important for operators to stay updated on the latest safety guidelines, regulations, and advancements in machine technology. Manufacturers or safety organizations may offer refresher courses or update training sessions to ensure operators are aware of any new safety features or procedures.
Internal Safety Programs: Companies employing nonwoven cut machines can establish their own internal safety programs. These programs may include regular safety meetings, safety audits, hazard assessments, and ongoing training initiatives. In-house safety trainers or experienced personnel can conduct specific training sessions tailored to the company's operating environment and safety protocols.
Operators should actively participate in training sessions, ask questions, and seek clarification to ensure they have a thorough understanding of the safe operation of nonwoven cut machines. They should also follow all safety guidelines, wear appropriate personal protective equipment (PPE), and report any safety concerns or incidents to their supervisors or safety personnel.
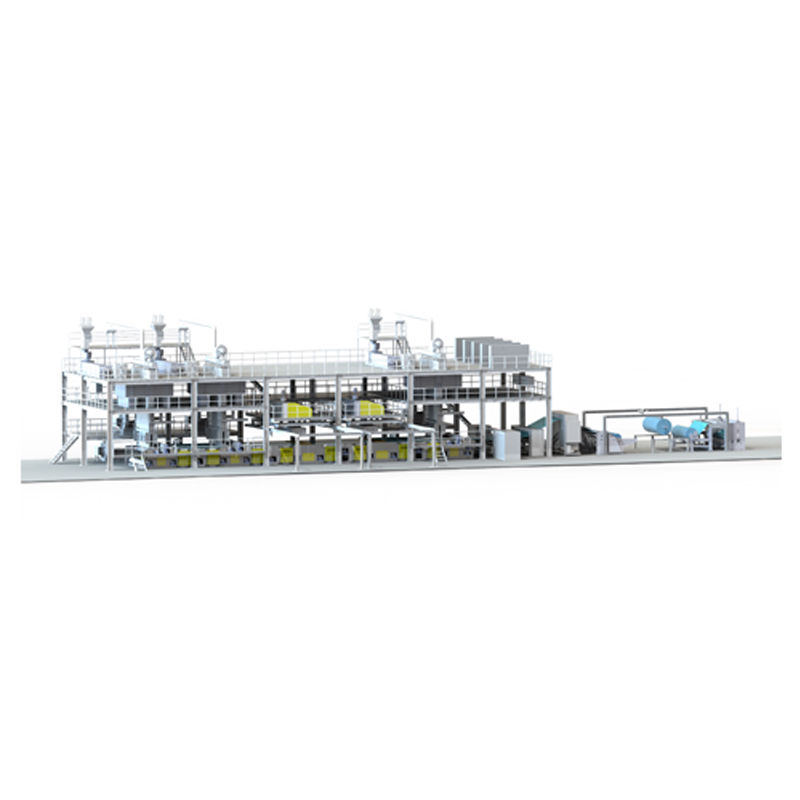